
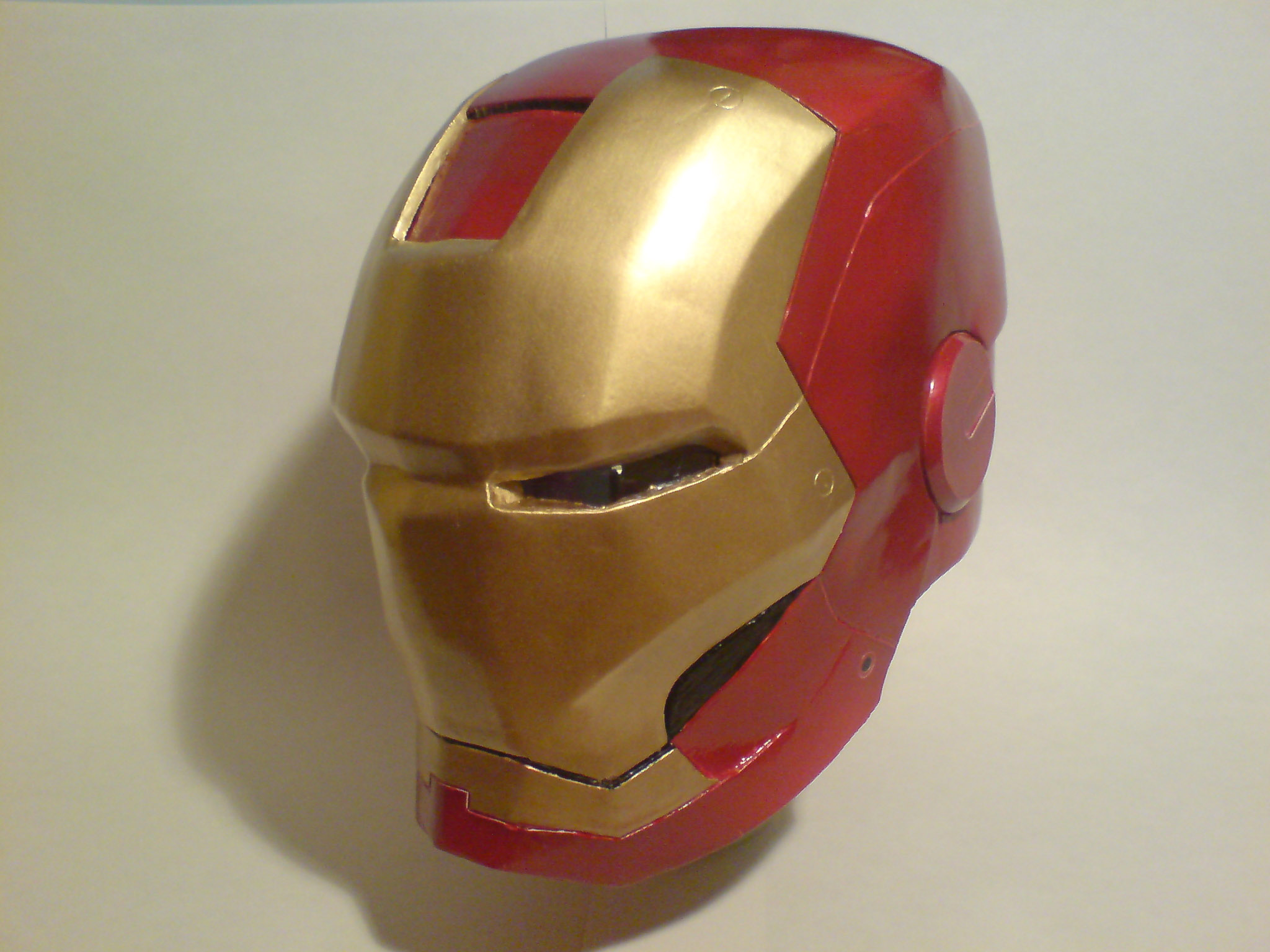
The second picture is what resulted from that printing. I went back to my original files and did some more thickening, bulking up the whole thing to the. If I had further subdivided the model, these blocky areas would have been less prevalent. As you can see in the second picture, you can still see some of the tessellation from modeling. The faceplate was thick enough and didn't end up warping. The bottoms were thicker than the top which ended up distorting. You can see this in the uneven color of the helmet halves. Because of the varied thickness, some parts hardened faster than others.
#IRON MAN HELMET CRACKED#
Because the helmet pieces were too thin, they warped, buckled and cracked while in the oven. When the pieces were printed, they were coated with a hardener/epoxy resin then put into the oven to cure.

Several days later, I got a call that the pieces were finished but there was some damage. When I was happy with the way the pieces fit within the box, I deleted the box shape, exported the stack as an STL file and sent it off the the prototyping group. Unfortunately, I don't have and pictures of the helmet being printed. As you'll see later, I could have gone even further with this step. When I was done adjusting the silhouette of the low poly helmet, I subdivided the model to provide a smoother finished surface.

That way, the sides and bottoms of the grooves would have extra material around then to prevent fractures. The final helmet varies in thickness because while the outside has grooves and ridges, I wanted the inside to be smooth. Because I planned on wearing this, (and probably walking into walls/doors/people) I wanted it to be thick enough the handle a bit of abuse. Thickness is important, it provides stability to the final product which can be brittle when it is printed too thin. The first step, while the poly count was low, was to extrude the model inward to give the helmet thickness. The conversion process was easy, but because the pep file is meant for paper usage, it was relatively low resolution and had no thickness.
#IRON MAN HELMET FULL VERSION#
With a full version that allows you to create files rather than just view, I exported the pepakura file as an OBJ which I could would with in Maya. I had also purchased a copy of the Pepakura software. :)Īs I mentioned, I had gotten the pepakura helmet file from the RPF forum. Please credit the Replica Prop Forum and I, if you use! As I outline in Step Two, the build envelope of the printer that was used to produce this helmet was 10" x 14" x 8", so I had scaled the pieces to fit that and it is sort of a happy accident that it worked out.
#IRON MAN HELMET ZIP#
I've added separate zip files with OBJ and STL files of the Ironman helmet pieces for others to use. I took photos and screen caps along the way, but I may have missed a few steps that I'll just have to explain. This is my first instructable, but I wanted to share my process for anyone who has been interested in going this route. I had tried building the helmet with pepakura files produced by a member of the, but I found I did not have the time/patience/skill to sit and trim out hundreds of pieces of paper and reassemble them. Early last year, before The Avengers came out, I approached the rapid prototyping department at my company and asked if they would be able to help me produce a replica Ironman helmet.
